Breadcrumb
Parameters Affecting Mechanical and Thermal Responses in Bone Drilling: a Review
What is it?
Research looking at the current techniques of bone drilling and examining the parameters and effects of bone structure, drill-bit geometry, operating conditions and material evacuation (removal).
What problem does it aim to solve?
Surgical bone drilling is performed for a variety of reasons including installing prosthetics and correcting bone fractures. Making sure that drilling doesn’t cause further damage — be it from the force of the drill itself or from the heat generated during drilling — is critical.
How does it work?
The researchers looked at multiple factors involved in drilling and their effects on the bone being drilled: thrust force, torque, heat accumulation/dissipation, cutting direction, bone density, the thickness of the bone’s outer layer, drill rotation and feed rate, drill bit shape, angles and wear and techniques used.
What are the real-world implications?
A set of recommendations emerged from this review. “In general, a point angle of 70–90 or 120–140 and a clearance angle of 12–15 can provide lower friction with unworn cutting edges in bone drilling. A helix angle of 24–36 is also recommended to reduce the risk of chip clogging during bone drilling. The chips generated during bone drilling can increase friction and temperature significantly if not evacuated efficiently. Using coolant fluid as external irrigation can help both chip clogging prevention and temperature elevation reduction, assisting chip evacuation. Intermittent drilling can be used for better chip evacuation, especially from deeper holes. For implantation, predrilling can reduce the maximum forces and temperature significantly. The recommended diameter of the pilot hole in predrilling is the inner diameter of the insertion screw.”
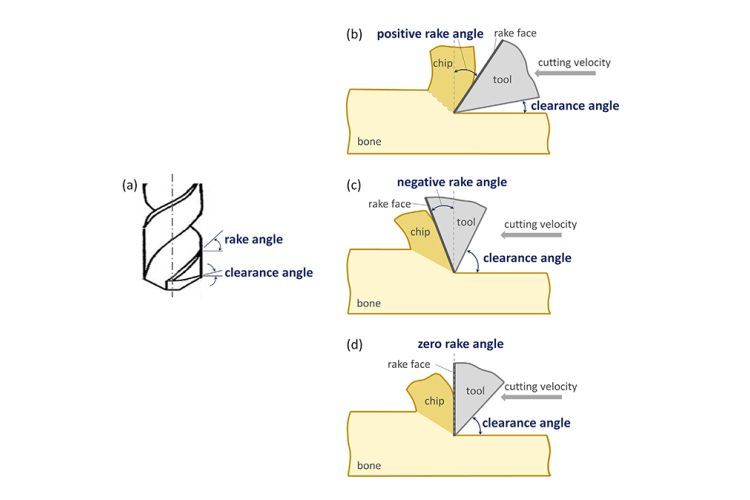
Fig. 6. Rake and clearance angles of a twist drill bit: (a) geometry of rake and clearance angles; (b) positive rake angle; (c) negative rake angle; (d) zero rake angle.
What are the next steps?
A larger, more comprehensive study would be the logical next step. In the meantime, dentists can start putting some of these recommendations into practice now, and students can learn from them as well.
Source
“Parameters affecting mechanical and thermal responses in bone drilling: A review”, Journal of Biomechanics, 71 (2018) 4–21
Authors
JuEun Lee and Craig L. Chavez, Department of Mechanical Engineering and Computer Science, University of the Pacific, Stockton
Joorok Park, Department of Orthodontics, University of the Pacific, Arthur A. Dugoni School of Dentistry